Due to the entangled molecular chain structure, high viscosity, and virtually no fluidity of ultra-high molecular weight polyethylene (UHMWPE), it is extremely difficult to process. Conventional processing equipment cannot easily form products from this material. Currently, most UHMWPE liners are manufactured using sintering compression molding, and some are made via plunger extrusion, though the latter has very low productivity.
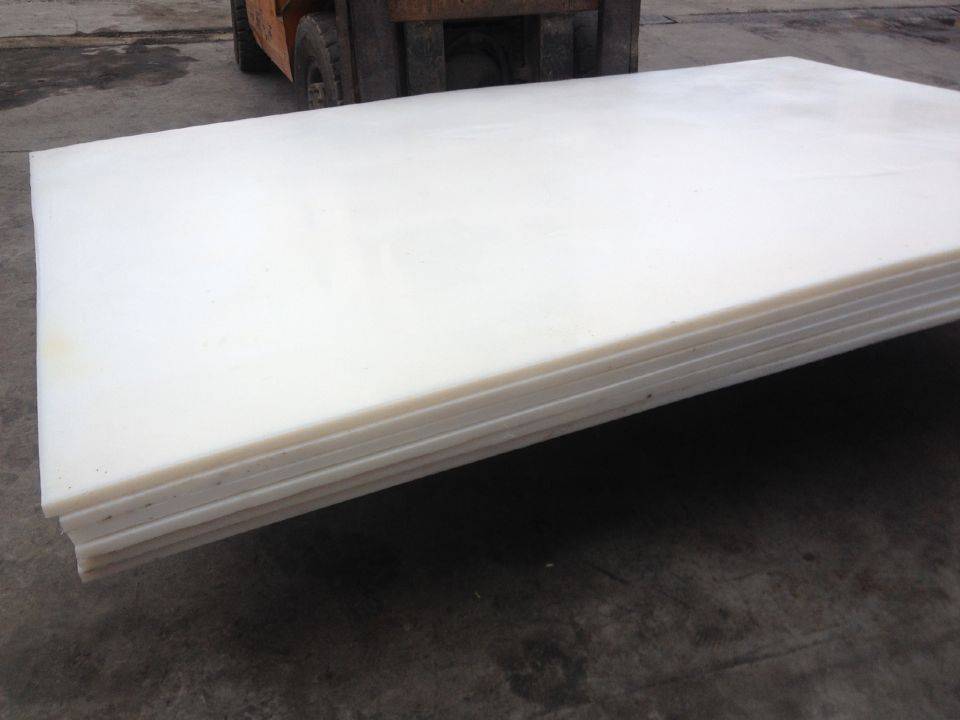
Key Features of UHMWPE Liners:
- Excellent Wear Resistance: The higher the molecular weight, the better the wear and impact resistance of the material.
- High Impact Strength: Outstanding resistance to strong external forces.
- Self-Lubricating: Ideal for applications in coal bunkers, chutes, grain silos, and hoppers—facilitates fast sliding of materials.
- Extremely Low Water Absorption: Mechanical properties remain unaffected by humidity in operating environments.
- Chemische Stabilität: Resistant to acids, alkalis, salts, and various organic solvents within certain temperature and concentration ranges.
- Non-toxic and Odorless: Inert and biocompatible, with no corrosiveness.
- Nicht klebende Oberfläche: UHMWPE has zero water absorption and a smooth surface, preventing material buildup.
- Excellent Low-Temperature Performance: Even under liquid nitrogen (-269°C), the material retains considerable mechanical strength.
Manufacturing Process of UHMWPE Sheets (Compression Molding)
When producing UHMWPE sheets via compression molding, the typical process involves the following steps:
- Raw Material Selection
The quality of raw materials directly affects the final product. High-quality resins with a molecular weight above 3 million, combined with scientifically formulated additives and optimized processing, are essential for premium sheet products. - Mixing and Pre-Blending
Raw materials are tested for quality (verifying inspection reports). According to a defined formula, additives are added and mixed in a high-speed mixer under specific temperature and pressure. This ensures uniform mixing and moisture removal. If colored sheets are required, pigments are added during this step. - Pressurization and Plasticizing
The blended material is placed into a mold, pressurized to remove trapped air, and then heated to melt the polymer into a translucent paste. The mold is held at a stable temperature and pressure to ensure full plasticization. - Forming
After plasticization, the material is gradually cooled while increasing pressure. The lower the temperature, the greater the pressure applied—until the processing requirements are met. - Demolding and Shaping
Once removed from the mold, the sheets are manually trimmed and shaped, then placed into storage for shipment.
Applications of UHMWPE Sheets:
- Paper Machinery
Water box covers, flow guides, dewatering blades, and foils. - Food Machinery
Guide rails, star wheels, guide gears, rollers, bearing liners, etc. - Chemische Industrie
Sealing plates, sealing materials, vacuum molds, pump parts, bearing bushings, gears, sealing interfaces. - Lining Applications
Coal bunker liners, hoppers, chutes, wear-resistant plates, brackets, backflow components, sliding surfaces, drums. - Andere Anwendungen
Agricultural machinery parts, ship components, electroplating industry, and low-temperature machine components.